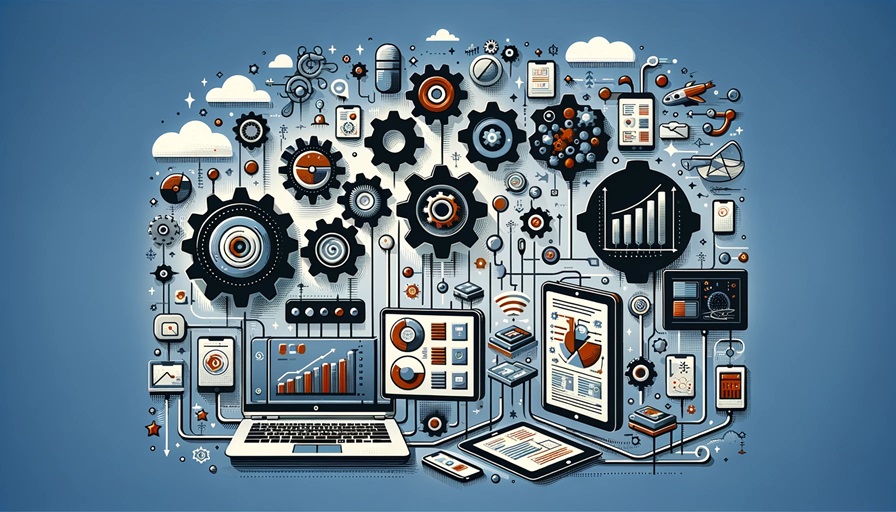
In the high-stakes arena of business, the spotlight often shines brightest on the glittering end-products: the revolutionary services, the breakthrough products, the customer experiences that redefine industries. This is the narrative that captivates audiences, the glossy, finished picture that businesses love to showcase. It's the story told in boardrooms and marketing campaigns, an alluring distillation of a company's essence into a few powerful words.
However, this outward narrative, as compelling as it is, skims only the surface of a deeper, more intricate saga. This is the story of the internal mechanics of your organization – a complex labyrinth of processes and systems, meticulously working in concert to breathe life into those headline-grabbing end-products. These internal processes are the unsung symphony behind the soloist, the intricate dance of cogs and wheels behind the curtain that orchestrates the seamless magic on stage.
In this narrative, the real protagonist is the relentless pursuit of excellence in these internal processes. It's about recognizing that the backbone of any successful organization isn't just what it sells or offers, but how it operates. Improving these internal mechanisms isn't just a task to be checked off; it's an ongoing journey towards operational nirvana, a commitment to excellence that fuels sustainable growth, innovation, and competitive edge.
So, as we delve deeper into the realm of internal processes, remember: you're not just tinkering with the mundane. You're fine-tuning the engine of your enterprise, setting the stage for a performance that transcends the ordinary. Welcome to the world where true business alchemy happens – welcome to the art of mastering and enhancing your internal processes.
What is an Internal Process
In the intricate tapestry of a business, internal processes are the essential, unseen threads that weave together the day-to-day operations. These processes are a series of interconnected actions, tasks, and steps, meticulously designed to achieve specific goals within the company. Much like the vital arteries in a living organism, they are crucial yet often hidden, playing a pivotal role in maintaining the health and success of the business.
Consider the analogy of a restaurant: the diner enjoys the final product - the meal. But behind this end result is a series of internal processes: sourcing ingredients, cooking, serving, and cleaning up. Each of these steps, while not directly observed by the customer, is critical to the dining experience. Similarly, in any business, internal processes encompass everything from manufacturing and quality control to human resources and inventory management. These are the internal blueprints, guiding employees in their daily roles and responsibilities.
What sets internal processes apart is their self-contained nature within the organization, functioning independently of external business partners. They form the foundation of a company, driving its success from within. These processes range from routine operational tasks to complex strategic initiatives, each contributing to achieving the company's overarching objectives.
The design and oversight of these processes are vital. They are not static but dynamic, evolving with the changing needs and strategies of the business. Managers and team members continuously refine these processes, ensuring they align with and support the company's goals. To measure their effectiveness, tools like the Balanced Scorecard are employed, offering insights into both financial outcomes and operational efficiency, and highlighting areas for improvement.
In essence, internal processes are the unseen yet indispensable cogs that keep the business machine running smoothly. They are the silent orchestrators of success, vital to the seamless functioning and growth of any organization.
How to Improve Your Internal Processes
Improving internal processes requires a meticulous and strategic approach, where every step is thoughtfully planned and executed. Let's take a look into a more in-depth, step-by-step plan that provides actionable strategies and considerations for each phase of the process improvement journey.
1. Prioritize Areas to Improve
First things first: identify which business processes need an overhaul. This isn't a quick glance over your operations; it's about diving deep. You're looking for areas that, when improved, will significantly boost your business.Â
Here's how to go about it:
- Conduct a Comprehensive Review: Dive deep into each business process. Utilize analytical tools such as SWOT analysis to not only identify immediate issues but also uncover potential opportunities for improvement. This involves assessing the severity of each problem and understanding its impact on your operations.
- Engage Stakeholders: Incorporate insights from a variety of stakeholders, including employees, customers, and possibly suppliers. Their perspectives are invaluable in revealing hidden challenges and suggesting areas that are ripe for enhancement. This also helps in considering your ability to address these issues, leveraging the strengths within your organization.
- Cost-Benefit Analysis: Carefully evaluate the investment required against the potential benefits of addressing each issue. This includes thinking about both the immediate and long-term returns on your investment, and the overall impact on your business’s growth and efficiency. This step is crucial in understanding what's going to give you the best return on your investment.
- Consider Ripple Effects: Keep in mind the interconnected nature of business processes. Improving one area might positively affect others, leading to a domino effect of positive changes across the business. This aspect is important in ensuring that the improvements resonate well beyond the immediate areas of improvement.
 It's important to remember that this process isn’t isolated. You're aiming for improvements that will resonate across your business, creating a domino effect of positive change.
2. Map & Document Your Current Processes
Mapping and documenting your current processes is a critical step in understanding the nuances of your business operations. If you haven't got detailed documentation yet, now is the perfect time to start. This stage goes beyond just noting down what you believe happens; it's about capturing the actuality of your day-to-day operations. Here’s how to deepen your approach:
- Break down each process into its individual steps. This isn’t just about listing actions; it’s understanding the flow, the interaction between different steps, and the dependencies that exist. Ask questions like, “What triggers this step?” or “What is required for this to happen?”
- Document not just who is involved at each stage, but also delve into their roles and responsibilities. Capture the resources they use, from software to equipment, and how these tools integrate into the process. This is about recognizing the human element and the material needs in your processes.
- Enhance your documentation with various visuals like flowcharts, diagrams, or even videos. These can provide greater clarity and help visualize complex processes. Consider creating process maps that show the sequence of actions and decision points.
- It's important to note and capture any variations in the process. How does the process change under different circumstances? Documenting these variations can reveal hidden inefficiencies or alternative pathways that may not be immediately obvious.
- Sometimes, the best way to understand a process is to observe it in action. Spend time on the ground, watching how the process unfolds in real-life situations. This can often reveal discrepancies between what's supposed to happen and what actually happens.
- As you document the processes, create a feedback loop with those involved. This allows for real-time updates and corrections, ensuring that your documentation is as accurate and comprehensive as possible.
Once you have thoroughly documented these processes, it’s essential to validate this information against real-world practices. This validation is a reality check to ensure that your documentation accurately reflects the actual workings of your business. By doing this, you lay a solid foundation for the upcoming analysis and assessment phase.
3. Analyze & Assess Your Current Processes
With accurate documentation in hand, you can start to dissect each process. This is where you take a step back and look at the bigger picture:
- Are the processes meeting your expectations?
- Where are the gaps between expected and actual performance?
Switch gears to a bottom-up approach, where you delve into the nitty-gritty:
- What could be causing the main problems within each process?
- How are these factors interconnected?
Creating a fishbone diagram using the 6Ms of Six Sigma can be incredibly helpful here. It allows you to visually map out potential causes and how they relate to each other.
4. Set Clear Goals
Now it's time to set specific, measurable, attainable, relevant, and time-bound (SMART) goals for your improvement initiative. For instance, if you're looking to reduce invoice errors, ask yourself:
- How much do you want to decrease errors by (a specific number or percentage)?
- What counts as an error, and how will you track them?
- Is your goal achievable with the resources you have?
- How does reducing invoice errors help your business?
- What's your timeline for achieving this goal?
Clear, SMART goals give you a roadmap to follow and make it easier to measure your success.
5. Plan & Implement Change
With your goals set, it's time to roll up your sleeves and get to work. This might mean small tweaks or a complete overhaul of your internal process. The key here is to:
Here are key steps to ensure effective change management:
- Ensure your team is fully prepared for the upcoming changes. This goes beyond just giving them the necessary resources; it involves providing comprehensive training and support. Create detailed training sessions that cover new procedures and policies. Consider different learning styles and include hands-on training, workshops, or e-learning modules.
- If your plan involves new technology, introduce it carefully. Provide demonstrations and training sessions to help your team understand and adapt to these tools. It's important to choose technology that integrates well with your current systems to minimize disruption.
- Before rolling out changes across the entire organization, conduct a pilot test. Choose a small, controlled group to implement the new process. This testing phase allows you to gather feedback, identify any issues, and make necessary adjustments before a full-scale implementation.
- Keep open lines of communication throughout the transition. Regularly update your team about the progress, challenges, and next steps. Encourage feedback and create a platform where employees can voice their concerns and suggestions.
- Establish a support system to assist employees during the transition. This could be a help desk, a dedicated team, or additional resources readily available to address challenges as they arise.
- As you implement the new process, continuously monitor its effectiveness. Be prepared to make adjustments based on real-time feedback and the performance metrics you've set. This flexibility is crucial for adapting to unforeseen challenges and optimizing the process.
- Recognize and celebrate milestones as you progress through the implementation. This helps in keeping the team motivated and acknowledges the hard work they are putting into adapting to the changes.
Remember, effective change management is not just about implementing new processes; it's about guiding and supporting your team through the transition. Keeping them motivated and involved is key to a successful transformation.
6. Automate Where Possible
After planning and implementing the necessary changes, the next pivotal step is to identify opportunities for automation in your processes. Automation can streamline operations, reduce human error, and free up your team’s time for more strategic tasks. Here’s how to effectively integrate automation into your business processes:
- Begin by reviewing your newly updated processes to identify repetitive, time-consuming tasks that could be automated. Look for areas where automation can not only save time but also improve accuracy and consistency.
- Select automation tools that align with your business needs and integrate seamlessly with your existing systems. Whether it's workflow automation, data processing, or customer relationship management, the right technology can make a significant difference.
- Since your team will be using these tools, involve them in the selection process. Their input can provide valuable insights into what features are most needed and which tools would be the most user-friendly and effective for your specific operations.
- Start with automating a single process or a part of a process. This allows you to gauge the effectiveness of the automation, make necessary adjustments, and build confidence among your team before expanding to more areas.
- Provide training for your team to ensure they are comfortable and proficient with the new automation tools. Also, set up a support system to address any questions or issues that arise during the transition to automated processes.
- Continuously monitor the performance of the automated processes. Collect feedback from your team and use this data to optimize the tools and workflows, ensuring they are delivering the desired results.
- Once you have successfully automated initial processes and worked out any kinks, look for additional areas where automation can be beneficial. Gradually expand the scope of automation in your business, constantly seeking ways to improve efficiency and productivity.
By thoughtfully integrating automation into your business processes, you can achieve greater operational efficiency, enhance accuracy, and allow your team to focus on more strategic, high-value tasks.
7. Review, Solidify, & Document Procedural Changes
As your new processes begin to take shape and become part of the daily routine, it’s crucial to continuously monitor their effectiveness and impact:
- Â Regularly compare the outcomes of the new processes against your SMART goals. This helps in evaluating whether the changes are meeting the objectives you've set out.
- Â Introduce key performance indicators and metrics that are relevant to the new processes. These should be clearly defined, quantifiable, and aligned with your business objectives. Regular monitoring of these KPIs will provide objective data on the efficiency, quality, and overall impact of the changes.
- Actively seek out feedback from your team. Their insights are invaluable for identifying areas that are working well and those that need further refinement. Encourage an open dialogue where employees feel comfortable sharing their observations and suggestions.
- Once you've fine-tuned the processes, it's essential to update your documentation and internal knowledge base. This should include detailed descriptions of the new procedures, the rationale behind the changes, and any relevant KPIs and metrics. This documentation serves not just as a record but as a resource for training and future process improvement initiatives.
- Take time to reflect on the broader impact of these changes:
- How have these processes improved operations, and what can be done to enhance them further?
- What other areas of your business have benefited from these changes?
- How have these changes influenced employee productivity and morale?
- Where should your focus shift next to continue driving improvements?
- Recognize that process improvement is an ongoing journey. The business environment and technologies are constantly evolving, and so should your processes. Use the experience and insights gained to tackle the next area in need of improvement.
Incorporating these steps ensures that your process improvements are not only effective and sustainable but also adaptable for future enhancements. By continuously monitoring, reflecting, and updating your processes and their documentation, you create a dynamic environment where improvement is a constant endeavor.
The Benefits of Having Internal Processes and Improving On Them
Effectively managing and enhancing internal processes is not just a procedural necessity; it's a strategic imperative that offers numerous benefits. These improvements can lead to significant advancements in various aspects of a business. Here's a closer look at these benefits:
- Increased Efficiency and Productivity: Streamlining internal processes eliminates unnecessary steps and reduces the time and effort required to complete tasks. This leads to higher productivity levels and allows employees to focus on more value-added activities. For example, automating routine tasks can free up staff to concentrate on creative and strategic work.
- Improved Quality of Products and Services: Well-defined and optimized processes ensure consistency in the production or service delivery. This consistency is key to maintaining high-quality standards, reducing errors, and enhancing the overall customer experience. For instance, rigorous quality control processes can significantly reduce defects in manufacturing.
- Cost Reduction: Efficient processes use resources more effectively, thereby reducing operational costs. By identifying and eliminating inefficiencies, businesses can lower expenses related to time, labor, and materials. For example, streamlining supply chain processes can lead to significant savings in inventory and logistics costs.
- Enhanced Customer Satisfaction: A smooth internal operation often translates into better customer service. Faster response times, consistent quality, and reliable service all contribute to a positive customer experience, which is essential for customer retention and attracting new clients.
- Better Decision-Making: Improved processes often generate more accurate and timely data, providing valuable insights for decision-makers. This data-driven approach can guide strategic decisions and help in identifying new opportunities or areas needing attention.
- Employee Satisfaction and Engagement: Employees often find a well-organized work environment more satisfying and less stressful. Clear processes and expectations can lead to increased job satisfaction, higher engagement, and a lower turnover rate.
In summary, investing time and resources in developing and refining internal processes can bring about transformative changes to a business. It not only enhances current operations but also sets the stage for future growth, innovation, and long-term success.
Examples of Internal Processes
Before delving into specific examples, it's important to understand that internal processes are the gears that keep an organization running. They encompass a wide range of activities, each designed to ensure efficiency, compliance, and customer satisfaction. These processes are crucial in translating a company's strategy into actionable steps and measurable outcomes. From the way a company manages its operations to how it interacts with customers and adheres to regulations, each internal process plays a significant role in shaping the organization's overall performance and reputation.
1. Operation Management Processes
Operation management processes are the day-to-day activities that form the backbone of a company’s product delivery or service provision. For instance, in a manufacturing firm, this might involve the procurement of raw materials, overseeing the production line, ensuring quality control, and managing the supply chain logistics.Â
The goals here are multi-faceted: maximizing resource utilization, enhancing operational efficiency, reducing production time, and minimizing risks associated with supply chain disruptions.
2. Human Resources Processes
These processes revolve around managing the company's most valuable asset – its people. This includes recruitment and hiring, training and development, performance management, and employee retention strategies.Â
A key goal is to cultivate a skilled, motivated, and productive workforce that aligns with the company’s culture and objectives. For example, a tech company might focus on hiring innovative thinkers and providing continuous learning opportunities to keep pace with technological advancements.
3. Financial Management Processes
These processes encompass the management of a company's finances, including budgeting, accounting, financial reporting, and risk management. For a retail business, this could involve daily sales tracking, managing cash flow, and analyzing financial data to inform pricing strategies. The primary objectives are to ensure financial stability, optimize profitability, and make informed strategic decisions based on financial insights.
4. Customer Relationship Management (CRM) Processes
These processes are designed to manage the company’s interactions with current and potential customers. They include identifying target customer segments, lead generation, customer acquisition, and developing strategies for customer retention and loyalty. An e-commerce company, for instance, might use data analytics to understand customer buying patterns and personalize marketing efforts, aiming to enhance customer engagement and satisfaction.
5. Research and Development (R&D) Processes
In industries like pharmaceuticals or technology, R&D processes are vital for innovation and staying ahead of the competition. These processes involve conceptualizing new products or services, conducting research, developing prototypes, and testing for efficacy and market viability. The goal is to continuously innovate and bring new, competitive offerings to the market.
6. Compliance and Regulatory Processes
These are critical for ensuring that the company operates within legal and ethical boundaries. This includes adhering to industry-specific regulations, environmental standards, labor laws, and corporate governance principles. For example, a food processing company must comply with stringent health and safety regulations, necessitating processes for regular inspections and quality assurance checks.
Each of these internal processes, while distinct, works in tandem to create a cohesive and efficient operational system within an organization. They are not just tasks to be completed but are strategic in nature, each contributing to the overall success and sustainability of the business.
The Continuous Journey of Process Improvement
As we reach the end of our exploration into the realm of internal process improvement, it’s clear that this journey is both critical and ongoing. The steps we've outlined - from identifying areas for improvement, mapping and documenting current processes, to implementing change and continuously refining these processes - form a cycle of perpetual enhancement that drives businesses towards operational excellence.
Remember, the pursuit of improved internal processes is not merely a task to be checked off. It is a strategic endeavor that requires commitment, foresight, and a willingness to adapt. By embracing this journey, businesses can unlock a multitude of benefits: heightened efficiency, cost savings, improved quality, enhanced customer satisfaction, and much more. These improvements are not just about the immediate gains; they lay the groundwork for sustainable growth and long-term success.
In this dynamic business landscape, the ability to refine and evolve internal processes is not just an advantage; it's a necessity. It ensures that organizations are not just keeping pace but are ahead of the curve, ready to adapt to new challenges and seize emerging opportunities.
So, as you step back into the everyday workings of your business, carry with you the insights and strategies discussed here. Keep pushing the boundaries of what your processes can achieve. Continuously seek ways to enhance efficiency, foster innovation, and drive your business towards its full potential. After all, in the quest for business excellence, the journey of improving internal processes is never truly complete - it is an ongoing path to greatness.